Nearly a century ago, chemicals maker DuPont adopted the slogan “Better things for better living…through chemistry”. Our modern chemicals sector is global in scale, processing millions of tons of material every year, with its outputs — from paints to plastics to fertilizers — deeply embedded in countless high-volume products. The chemicals produced by this industrial production are so formative to our food system that we humans would not exist in our current billions without them.
In 1935, DuPont could describe chemistry as key to better living. Today, we can say that it is essential to modern living – to a world of today’s size, abundance, and variety. It is also a key, and challenging, part of our greenhouse gas emissions. The chemistry involved in chemicals production cannot be wished away, and replacing today’s approaches will require scaling lab bench experiments into the millions of tons of annual production. This is indeed a big challenge – and it’s imperative that we solve it.
This Voyager letter explores today’s chemistry sector, the challenges to decarbonizing chemicals production, the promising approaches that we see emerging, and the support and scale that will be needed for meaningful change.
Chemical Importance and Chemistry Challenges
Chemicals are essential to modern life, and we have (rightly) built massive, optimized systems to produce them as efficiently as possible within the limits of chemistry itself.
Chemicals production is dominated by two significant molecules by volume – ammonia and methanol – as well as a large and diverse class of high-value chemicals. Ammonia and methanol are simple, foundational molecules that are versatile as energy carriers and as inputs to other chemicals production. The high value chemicals serve as building blocks to make a range of ubiquitous commodity end products such as ingredients in shampoos, cleaners, and foods.
Ammonia, a compound of one nitrogen atom bound with three hydrogen atoms, is unique among the major chemicals in that it contains no carbon. It is a common chemical in nature, and a common nitrogenous waste, but it is also dangerous in its concentrated form. More than two-thirds of current ammonia produced today is used to make industrial fertilizer. Ammonia is made today using the Haber-Bosch process developed during WWI by German chemists Fritz Haber and Carl Bosch. Today, half the nitrogen in the human body – consumed by society in the form of food from industrial farms - now comes from synthetic ammonia fertilizers produced by the Haber-Bosch process. Beyond its traditional uses, ammonia could be used to help decarbonize a range of other sectors. It’s a molecule that is a stable energy carrier: it is energy-dense, can store energy indefinitely, and be shipped long distances. For these reasons, it could play a role in a much-expanded green hydrogen production and consumption system, as it’s easier to transport than hydrogen. As a result, it is often proposed as part of decarbonization approaches for heavy-duty transport, primarily maritime applications.
Methanol is the simplest alcohol molecule, containing one carbon atom, three hydrogen atoms, and one hydroxyl of oxygen and hydrogen. Methanol is volatile and flammable. Originally produced by distillation of wood (giving it its common name, wood alcohol), it is today made through low-pressure refining processes using catalysts. Methanol is used mostly as a precursor chemical for more complex molecules such as formaldehyde, which is then used to make polymers. Methanol is also a potential energy carrier molecule given its hydrogen bonds which once broken can release energy and hydrogen gas, but its volatility and its lower energy density (lower than ethanol and half that of gasoline) work against it in this role. Furthermore, use of methanol as an energy carrier will still release carbon dioxide when combusted, given its carbon atom, making it inferior to other carriers such as ammonia or hydrogen, which do not contain a carbon atom.
High-value chemicals are a family of compounds mainly used as chemical precursors for other important materials. Ethylene, propylene, benzene, toluene and mixed xylenes are chemical building blocks for a number of products such as plastics, glues, paints, solvents, resins, films, and more.
Global chemicals production has grown by 47% since 2010. Production has not grown evenly across chemical categories – ammonia production is lower today than it was in 2013. Methanol production, on the other hand, has increased 2.4 times since 2010, and high-value chemicals production has increased by more than 30% over the same time.
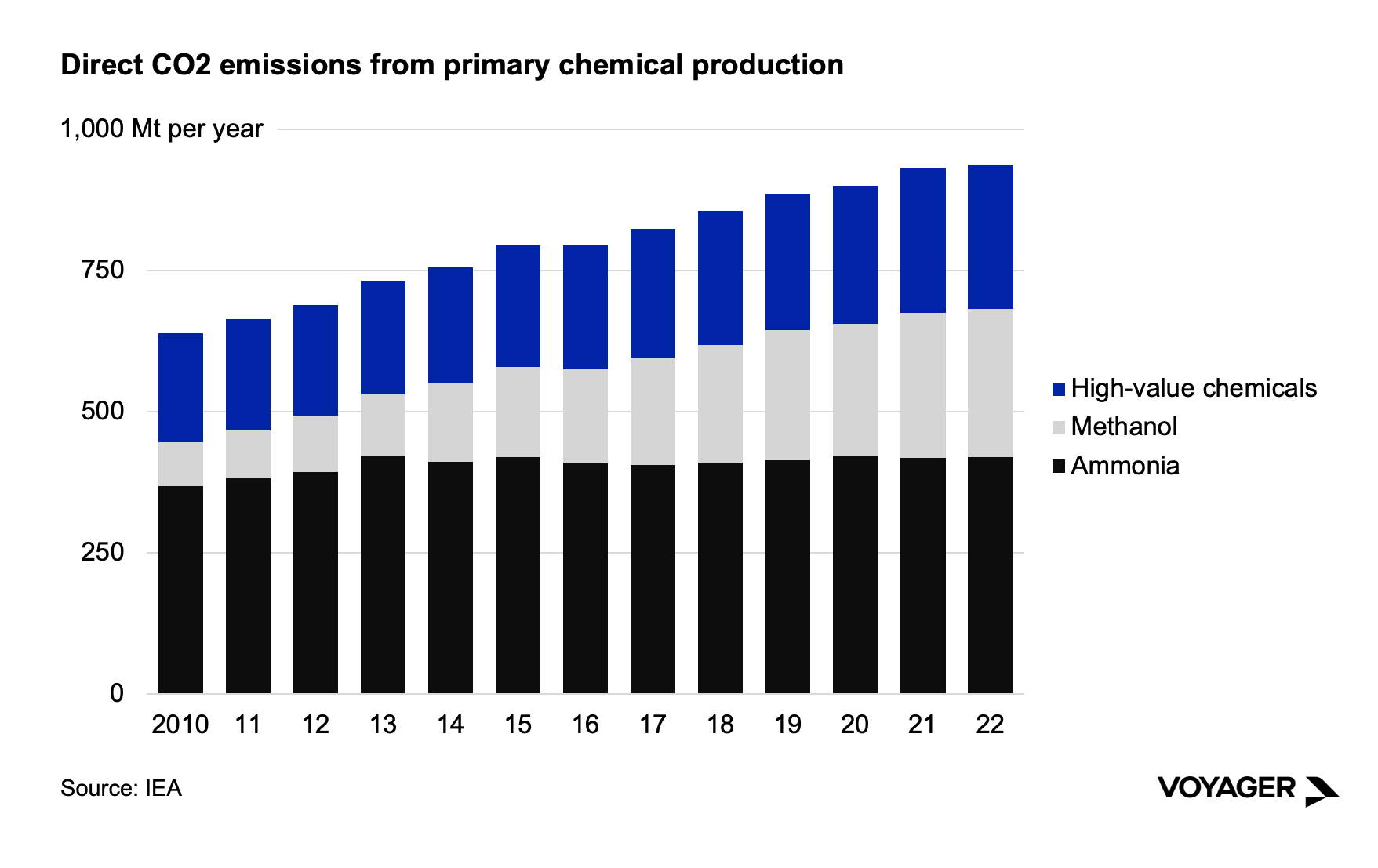
During the past decade, the emissions intensity of chemicals production has hardly budged. In fact, it has changed so little since 2010 that it does not even bear charting. In 2013, the carbon intensity of chemicals production was 1.30 million tons of CO2 for every million tons of primary chemicals (roughly 935 million tonnes of CO2 total annually in 2022) – and last year, the carbon intensity was 1.30 million tons of CO2 for every million tons of primary chemicals. The reason behind this is both simple, and profoundly important for decarbonization: about half of the chemical sector’s energy input is not burning fuel, but making feedstocks. These are the irreplaceable raw material inputs that will be chemically transformed into a wide range of chemicals.
This means that the addressable surface for decarbonization is fundamentally limited (compared to electricity, for instance, where zero-fuel, zero-emissions production is possible). That does not mean, however, that there are no avenues for decarbonizing chemicals production. There are many, with many promising new approaches to reimagining traditional processes.
Heat and Efficiency
Perhaps the most straightforward decarbonization effort for the chemicals sector is addressing its thermal energy inputs. Chemicals production requires heat (and often, pressure) to initiate and sustain chemical reactions. Today, that heat is mostly supplied by burning fossil fuels, often used to create steam at high pressure.
Heat, however, can be produced without combustion. Heat pumps, for instance, can extract waste heat from industrial exhaust gases or wastewater effluent streams to produce ample heat up to 200 degrees C, sufficient for some uses in distillation, reactor heating, steam generation, and heat pump assisted drying. Heat pumps are also three to five times more energy-efficient than gas-fired boilers. While heat pumps for residential heating have set new records in sales every year, particularly in Europe, they are still early in their widespread adoption, and it’s earlier yet for heat pumps for industrial waste heat, which are still in development.
Thermal energy storage is also promising. Thermal energy storage systems can store heat generated via electric induction at very high temperatures, up to 1,500 degrees C in some cases. Those temperatures are sufficient for almost all chemical production processes, and if the electricity providing the heat is zero-emissions, can completely decarbonize heat inputs.
There are also new approaches to decarbonizing not just heat creation, but chemical production processes themselves. Ethylene cracking, for instance, requires heating feedstocks with steam in a zero-oxygen environment to the point where larger molecules ‘crack’ into smaller ones. Today, there are plans to use electrically-energized ethylene crackers which consume no onsite fossil fuel.
And there are also efforts underway to optimize production processes and maximize process efficiency using artificial intelligence and digital tools. Specifically, AI is being used for process optimization and predictive maintenance using sensor data, but also for carbon accounting to identify GHG reduction opportunities and materials development to identify new chemicals, catalysts, sorbents, and membranes.
Capture and Feedstocks
Point-source emissions capture is another way to decarbonize chemicals production insofar as it’s possible to do so. Chemical transformation necessarily results in the creation of other molecules, some of which are greenhouse gas emissions in their own right.
Very large-scale efforts to capture gases – such amine-based capture of carbon dioxide post-combustion – have been deployed since the 1990s. However, they have not been deployed at sufficient volume today to make a meaningful impact on the sector’s emissions, and are themselves very energy-intensive to operate, meaning that they require their own substantial energy use.
Membrane-based approaches may be more promising for separating carbon dioxide and other GHGs out of a mixed flue gas stream. Several companies such as Osmoses, Unisieve, and Ardent are working on membranes with optimized pore sizes which may reduce the capital and operational expenditures which have limited the growth of point-source capture to date.
Feedstocks and Modularity
Another approach to decarbonizing chemicals involves feedstocks. These approaches vary, but all require substituting new molecules into transformation processes.
One approach is to use biomass in place of fossil fuels. Chemically speaking, the atomic composition of these materials is quite similar: biomass is a hydrocarbon, after all, and is itself the feedstock for producing oil, gas, and coal (albeit on timelines measured in millions of years). What’s different is the carbon footprint: as biomass grows – whether plant or other organic matter – it pulls down carbon from the air, making it a potentially carbon-neutral feedstock. Biomass feedstocks can potentially substitute for fossil hydrocarbons, though this will require custom engineering or re-design of processes built around a century of oil, gas, and coal inputs. Biomass, however, can be logistically intensive and limited in supply. Effective use of biomass to meaningfully substitute for fossil fuel feedstocks will require robust measurement, recording, and verification of embodied carbon to ensure additionality, and to make sure that biomass is not being diverted from food production or using farmland, and thus not driving up food prices.
Another feedstock approach is to use recycled materials, essentially reversing the production process which created plastics and textiles from chemical inputs. These processes would reduce the requirement for new feedstocks, but they are also complex, for several reasons. The first is that collecting recycled material in sufficient quantity and quality to serve industrial processes is already challenging. The second is that the recycling sector itself requires new technology to effectively process its intake. Absent strong and binding policy in major jurisdictions to enforce recycling and help drive down costs, recycling may play a limited role.
Carbon dioxide itself can even be used as a feedstock. The molecule is (unfortunately for the climate) more atmospherically abundant than at any point in the past three million years, and removing it for productive use would be very welcome. However, today’s large-scale carbon removal projects are still at the demonstration phase, and direct air capture technology, while improving steadily, is still a much more costly way to source feedstock than conventional sources. Furthermore, converting carbon dioxide into other useful chemicals requires material amounts of energy given the carbon-oxygen bond is one of the strongest of all molecular bonds.
Greening the world’s supply of hydrogen – another key chemical feedstock - is perhaps more promising. The world consumes 100 million tons of molecular hydrogen every year, most of it sourced from steam methane reformation of natural gas (so-called ‘grey hydrogen’, which results in carbon dioxide emissions). Green hydrogen is produced through electrolysis powered by zero-carbon electricity. Unfortunately, without subsidies, it is more expensive than grey hydrogen for the time being. Natural hydrogen, referred to as white or gold hydrogen, is hydrogen that occurs in natural deposits underground and could be extracted and used. It’s a new idea, and may play a significant role in decarbonizing chemicals production provided there are sufficient reserves which can be tapped, harvested, purified, and transported in an economically feasible way, and that leakage can be controlled.
Today’s chemical production system has grown through ever-greater scale. The Jamnagar complex in India (which combines a refinery with aromatics production, petrochemicals, power generation capacity, and a port and terminal) occupied a work site larger than London while under construction. However, tomorrow’s decarbonized chemicals production could come via the opposite approach – modular, decentralized production.
A number of startups are taking modular approaches to ammonia or nitrogen fertilizer production, such as Nium, NitroFix, Nitricity, Ammobia, and others. Their approaches can be simpler to produce and install than massive integrated complexes. Component parts, and even units, could theoretically be made in high volume and therefore benefit from manufacturing economies of number vs. economies of scale and therefore avoid megaproject economics. Production closer to demand centers could also reduce the often substantial emissions incurred in transporting chemicals from plant to demand center. In order for these modular approaches to thrive, they must ride down their cost curves sufficiently to provide a viable economic alternative to today’s status quo options.
Imperatives for Tomorrow’s Chemistry
Much of our global chemicals industry has been built to-date using thermochemical pathways that rely on heat, pressure, and catalysts. These systems are so robust that even the most promising emerging methods of decarbonizing chemicals will likely use existing, or similar pathways. What interests Voyager in particular, though, are the many ventures attempting to tap into innovations in thermochemical approaches and other pathways such as electrochemistry or synthetic biology for decarbonizing most of the chemical building blocks we use today.
We do not yet have conviction that emerging approaches can fully disrupt the established, optimized chemical production pathways that dominate today. But, the broad set of approaches that startups are pursuing today, and the potential scale of their operations if successful, are hugely promising for decarbonizing an essential sector in modern life.
One strategy for decarbonizing chemicals is clear to Voyager. Regardless of which pathways win in the race to produce commodity chemicals at lower costs than the fossil-fuel alternative, we will need the support of policymakers and large corporates. These two groups will be essential in providing new technologies a leg up in their early cost curve reductions via green-procurement mandates, subsidy, or carbon taxes. In certain cases, such as in recycling, policy may have to play an even larger role given the very low costs of virgin plastics and the complexity of the recycling and sortation infrastructure.
Today’s chemicals sector is well-established, deeply funded, optimized over a century of operations, and essential. Decarbonizing it, therefore, is a science challenge, but it is also a structural challenge, requiring new policies, new priorities, and deep and broad commitments to change. Entrepreneurs are doing their part, fortunately, and science is too.